Parts without draft cannot eject from the. There are some products however which are known to be susceptible to damage from vibration they might experience during transportation.
A Guide To Choosing Foam Packaging
For most products a package that provides protection against mechanical shock during shipment is all that is required.
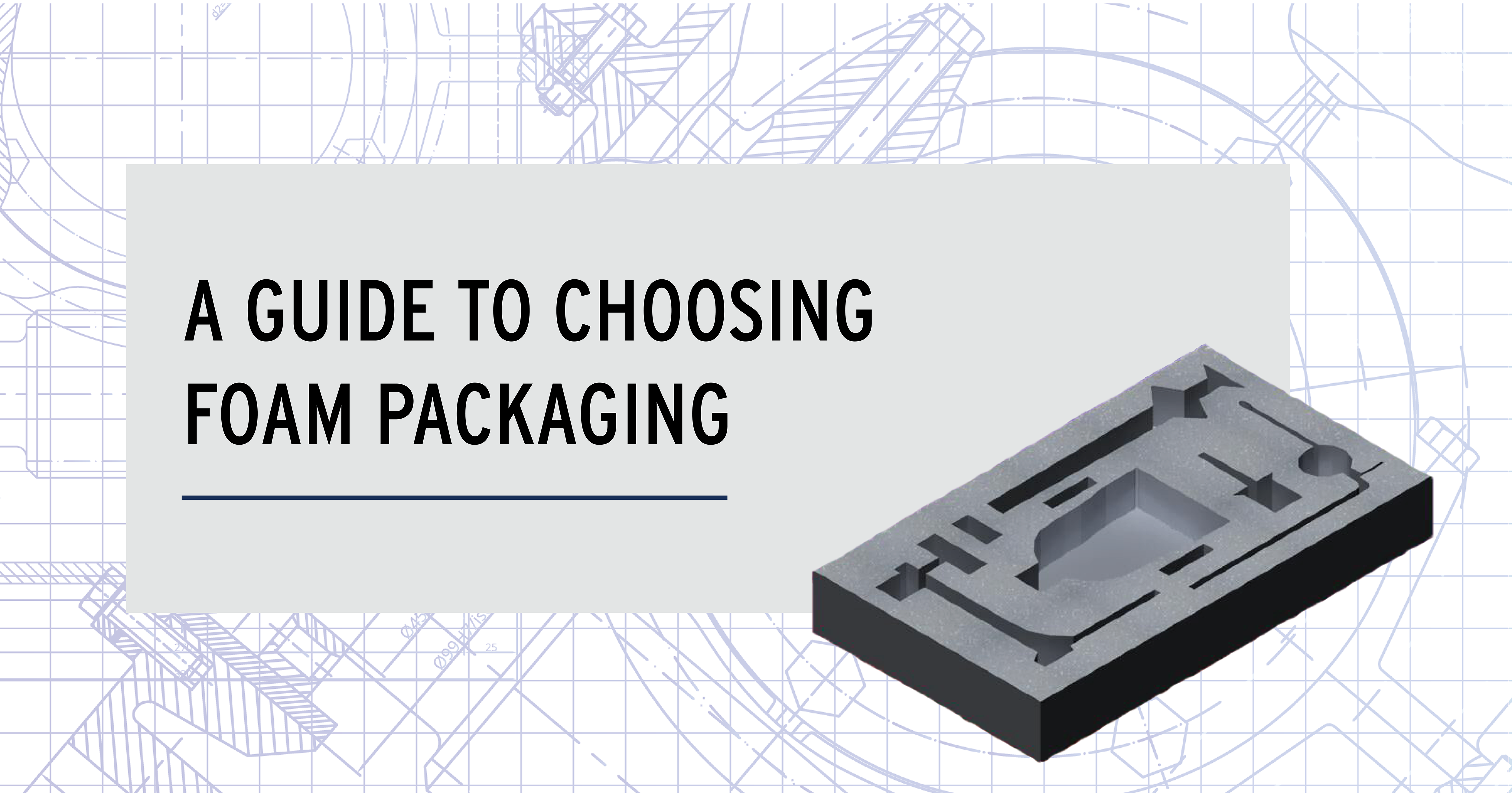
. Custom Foam Packaging Design For durability and resiliency flexible foam stands out. By incorporating molded-in features. Which type of packaging foam is best for your product.
For heavy products we can use high density EVA foam sheets to fabricate custom foam inserts. In this context system architecture refers to the logical arrangement of all components in a given 3-D volume. Inside and outside printing.
The Best Definitive Guide. Most part designs will require a minimum of 5 degrees of draft or radius to self-eject the part. Package Design Guide.
When you are considering a foam packaging design EVA foam could be your No1 option. Determine your products static loading on the foam psi. To start PSI is used to determine your foam density.
Three common foam types are as follows. Because the injection molded foam process utilizes self-ejection instead of the mechanical injection of thermoplastic injection molding one of the most critical design principles is using the correct draft. Ad Create product packaging theyll remember long after opening with poly bags.
It contains recommended considerations and procedures for the design and development of highly protective. Make a statement when sending soft goods and apparel shipments. Your cushion must be at least 21 inches wide or long to resist buckling.
Tapered heated dispenser minimizes cold-shots. Package Design Guide. Determine the fragility level of your product-using Chart 1 as a guideline.
Foam products can be found everywhere such as sofa chair tape insert packaging baby pay mat furniture and mattress upholstery. Full color quality mailers. This guide has been prepared to assist packaging designers in the selection and utilization of ETHAFOAM brand polyethylene foam and other Performance Foams products for protective packaging applications.
Todays innovative design engineers are capitalizing on the unique property profiles of foamable NORYL VALOX and LEXAN resins to design parts. We use the highest quality foams in our protective packaging solutions and can quickly accomodate high volume orders for short or long-run production at our state-of-the-art facility in Tempe Arizona. Foam is used to form items such as.
By varying the density thickness and shape of the EPS foam the designer can meet the protection. It contains recommended considerations and procedures for the design and development of highly protective and cost-efficient packaging. Foam materials are a quite.
This information is offered. For higher strength higher density ETHAFOAM products the use of a 075 buckling coefficient is recommended. EVA foam material is offered in various densities and colors and this makes it a very common and popular foam material for custom foam packaging insert.
Do this by dividing your products gross weight by the largest. Recyclability categories consider the impact of design features on the value as feedstock of a package the productivity of the reclaimers and the quality of the final post-consumer resin PCR or finished product application. When product fragility g-factor and handling environment drop height have been determined the procedure that follows can be used to determine the amount of functional cushioning material which will provide adequate protection for the packaged item.
Design Prototypes and Test. 01-03 PSI 2 lbft3 polyurethane 04-06 PSI 4 lbft3 polyurethane. 3x 07 21.
Foam Factor Once the fragility drop heights based on weight and PSI are established the foam type density and thickness can be determined. Determine your products static loading on the foam psi. Get our free guide to compare functionality and price points for four different types.
End-caps L-blocks corners trays and a wide variety of other shapes. Calculate Fundamental Cushion Requirements. Determine the fragility of your product using Chart 1 as a guideline.
Here we are going to introduce how foam fabricators utilize a wide range of amazing foam fabrication techniques to make all sorts of foam products. Lowest price or well match it on all stock sizes. In the preliminary design stages cushion curves developed from dynamic drop testing are used to determine the correct package configurationfoam thickness and densityto adequately protect the product.
Foam Packaging Specialties has been an industry leader in the foam packaging industry since 1976. Using the formula T x WT W you can now find the minimum width. The best way to take advantage of foam packaging is to work with a custom packaging designer to ensure youre using the proper foam for your specific needs.
The functional foam determinations made in conjunction with dynamic cushioning curves of ETHAFOAM. SmartShot - The standard handheld foam-in-place packaging system designed for small medium and large applications that require protective void fill blocking and bracing and cushioning during the shipping and handling process. The APR Design Guide addresses design features or components commonly used with plastic packaging applications.
Follow these easy steps. Each packaging design must be developed separately given the large number of variables involved. Structural foam molding process large load-bearing parts and assemblies can be produced with the optimum balance of functionality performance aesthetics and costs.
Insulated handle stays cool. Determine Conditions the Product Will Encounter. Package Design Guide This guide has been prepared to assist packaging designers in the selection and utilization of ETHAFOAM brand polyethylene foam and other Performance Foams products for protective packaging applications.
Ad Fastest turnaround - ships in 3 days. Do this by dividing your products weight by the largest surface area that will have contact with. Certainly no specific recommendations can be made about how to fabricate and position the foam on or around a particular product.
Upload a File Request a Quote Customer Login 1-800-659-8559. Elasticity produces memory capability making flexible foam parts resistant to crushing during repeated impacts. In most cases the outer dimensions and interfaces are driven by the industrial design.
Your packaging should be made to fit your product not the other way around and a professional designer will help you create the perfect solution. Foam Selection in 4 Easy Steps. Package Design Guide.
Once product fragility is determined the packaging designer should next consider the handling and transportation environment the product will face. As with most product designs designing with EPP begins with the mechanical architecture. To establish the amount of shock the product may encounter it is necessary to determine the height from which the.
Foam Packaging Insert Best Selection Guide Foamtech
Foam Packaging Insert Best Selection Guide Foamtech
Bio Cushion If World Design Guide
Foam Packaging Insert Best Selection Guide Foamtech
The Guide To The Benefits Of Foam Packaging Jamestown Container Corrugated Packaging Solutions
0 komentar
Posting Komentar